Is your fleet operating as efficiently as possible? Do you gauge its performance against benchmarks and industry best practices? With the emergence of advanced data analysis and innovative technology within the fleet landscape, such as telematics, AI, and alternative energy sources, today’s managers must transition skills and develop new strategies to become the best-in-class, reduce costs, and improve safety and drive sustainability.
Here we will discuss fleet solutions including crucial measurements and tools to help strengthen your Fleet Wellness®, efficiency, and performance.
1. Repair & Maintenance Costs
Increasing repair costs could be a sign you are holding on to vehicles too long. Had you disposed of your vehicles one year earlier, you could have avoided that expensive repair. High maintenance costs could indicate that you are over-maintaining your vehicle. Ensuring both preventive maintenance is performed and ongoing repairs are tracked is critical to Fleet Wellness.
2. Fuel Costs
By tracking your fuel consumption, you can quickly identify a myriad of problems common to vehicle fleets, including maintenance issues, poor tires, improper driver behavior and inefficient driving routes. Tracking fuel consumption and expenditures can also help determine which brands and models provide the best fuel economy in real-world situations; most commercial vehicles are not rated or required to be rated, for fuel economy by the EPA.
3. Availability of Your Fleet
Everyone likes to quote availability percentages, and in today’s data-driven climate, a wash of information is available for managers to measure their effectiveness with little difficulty. The amount of data, however, has little meaning unless it is collected, analyzed, and interpreted.
Several metrics can best help you measure and analyze the availability of your fleet; consider vehicle downtime, vehicle idle time, and the duration of time between repairs in comparison to your fleet’s total time available.
4. Driver Risk
Driver behavior and safety can be measured and tracked allowing management to address risky behavior, wasted time/fuel, and reduce accidents. Risk management tools include a driving policy, driver testing, and telematics. Each can help reduce your fleet’s risk. There are several ways to measure the impact including the following:
- Total number of accidents per 100 hours of driving
- Insurance cost per vehicle
- Repair costs per vehicle
Fleet Solutions
After you’ve gathered and analyzed the data from measuring your fleet’s performance, identify inefficiencies and problems with your fleet. What do you do about them? Well, there are multiple fleet solutions available to optimize your fleet’s productivity and efficiency.
Managed Fleet Maintenance Programs
Under a managed fleet maintenance program, companies pay for the actual cost of the repairs, plus 10% for the management of the program. Companies experience 30-40% cost savings under a managed maintenance program versus a non-managed program.
How? The following list of solutions all exemplify the amenities offered by managed fleet maintenance programs, as well as the long-term benefits that companies experience as a result.
Preventative Maintenance
The best approach for vehicle repair is one that emphasizes prevention. Preventing problems before they appear, not only drastically reduces repair costs over time but also significantly lengthens vehicle lifespan.
Preventative maintenance programs also manage factory warranties, ensuring a company will never pay for components that are already covered by warranty. This process is both fleet tested, and client approved.
Vehicle Maintenance Schedule
Customized vehicle maintenance guides (VMGs) are prepared for every vehicle in the fleet. The vehicle maintenance schedule appears in graph format and illustrates different vehicle components that require routine maintenance and how often these parts should be addressed. Among the items on this list are oil, lubrication, filter changes, checking and adjusting brakes, transmission service, coolant service, tire rotation, tire pressure checks, fluid level checks, fuel filter changes, and more.
Established Vendor Network
Managed fleet maintenance provides access to an established nationwide vendor network. With more than 50,000 national account facilities and 7,000 independent repair facilities, service is never far away. Even more, a network rating system displays the top rated vendors and reviews on independent repair facilities.
Customer Contact Center
Managed fleet maintenance includes access to a toll-free, 24/7 customer service line. You can use this amenity to receive immediate attention from an on-staff ASE mechanic who can offer counsel on the best available repair shops near you.
Repair Process
The repair management process with managed fleet maintenance is straightforward. The driver who experiences a problem contacts the customer care center, where a certified technician captures detailed information about the vehicle and locates a nearby repair facility.
Once in the shop, they contact network specialists to see if the repair is necessary. The driver never has to deal with the stress of determining repairs on behalf of the company, nor has to negotiate the repair cost. The network specialist takes care of both of those things for them.
Detailed Reporting
No more manila folders and manual tracking via spreadsheet; managed fleet maintenance programs include detailed reporting. You can choose the timeline and format of these reports as well, with options including online, monthly, quarterly, and annual reporting. It also features line item detail, which allows for a drill down from summary reports.
Fuel Programs
With tools such as exception reporting and fleet fuel cards, you can quickly identify all the problem areas of your fleet. A proactive fuel management program helps control cost, improve driver productivity, meet regulatory requirements, and provide for the collection of essential data used for management reports.
A typical fuel management plan issues one fuel card per vehicle, as well as a unique pin number for each driver. The card is only valid for fuel purchases, and a driver must enter the mileage and their pin number to enable the fuel pump. The unique codes allow data to be collected for each vehicle and driver, including mileage, grade of fuel, and fuel economy. Thus, it can identify drivers that fill up with mid-grade or premium fuel, or whose fuel economy is below average. The data captured from fuel programs also drive push notifications for preventative maintenance.
If your company doesn’t have a fueling policy, here are several quick tips to help your company create one.
Communication: Once you’ve established your fleet fueling policy, clearly communicate the new system to every driver in your fleet. Also, raise driver awareness, and in turn responsibility, by informing your team that fuel consumption and purchases are being monitored and that all exceptions, especially repeated infractions, will need to be justified.
At The Pump: Whether it’s with premium or mid-grade fuel, filling a vehicle’s tank can cost your company as much as 25 cents more per gallon. This can add up over time. Establish the desired grade of fuel for each vehicle and have a process in place to monitor it. To further enhance your fuel management program, enforce limits at the time of purchase. If you restrict drivers, for example, to two transactions per day, their fuel awareness and efficiency will not only increase, but also benefit your fuel management system and controls. Many fleet managers also benefit from placing restrictions on non-fleet fuel products and services. By regulating your drivers’ use of their fuel card on items such as soda, coffee, or car washes, you can better control costs, quality, and consistency at the pump.
Location: By monitoring the location, days, and times of fuel purchases, you can mitigate the costs and abuse problems associated with drivers refueling outside of regular business hours. On top of evaluating purchases that consistently exceed fuel tank capacity, map out en route fueling stations that offer high-quality gas at an affordable price. Once you’ve identified and shared these locations with your drivers, encourage them to “pay-at-the-pump,” as this will help them save time, reduce idling, and get back on the road.
Telematics
Telematics is vehicle tracking technology, important for addressing driver risk, fuel use, risk management, efficiency and more. With telematics, you receive a variety of notifications such as maintenance alerts and driver behavior to ensure safety and manage your fleet needs.
Maximizing Efficiency and Effectiveness
Many fleet managers have seen how fleet solutions offered by third-party fleet management companies leads to more time for the fleet manager to focus on the daily challenges that occur. Fleet management companies provide additional insights and expertise and introduce a full team that reduces the risk when your staff members are out sick, on vacation or leaving the organization.
Fleet management companies have seasoned professionals that work across industries, study and implement current technologies, understand how to provide management with an ROI analysis for newer vehicles and save money, and deliver new ideas that help your business grow.
Other benefits offered by fleet management companies:
- Experience with Telematics: Professionals can interpret data and create controls based off of a range of gathered information.
- High Returns: Fleet management companies offer fuel and maintenance programs that can help save your business up to 40% of fleet-related costs. They also provide flexible leasing options to help you save tax dollars and improve cash flow.
- Advisors: By combining fleet solutions with both short and long-term company goals, fleet management companies can optimize your entire operation.
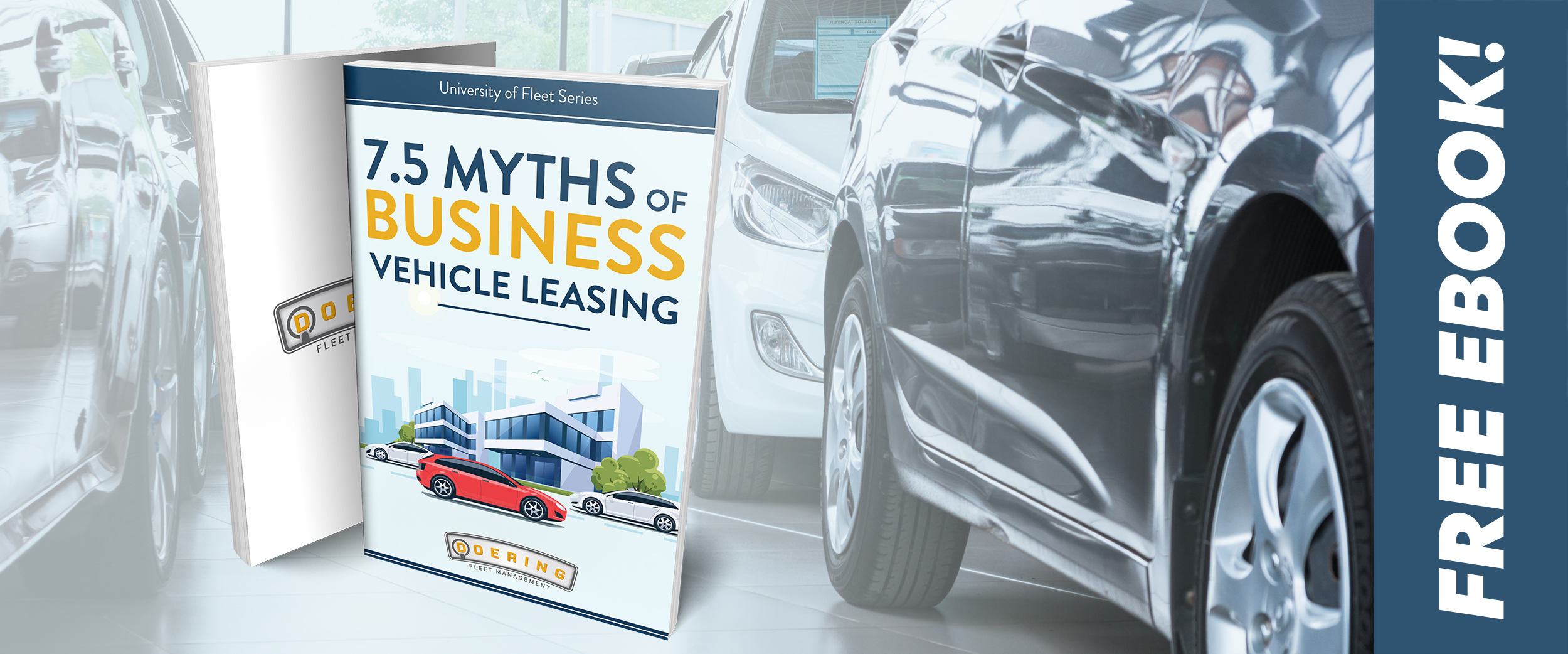